Precision CNC machining aerospace components carries the burden of human belief in each gram and micron. Because the race for lighter, fuel-efficient plane and Mars-ready rockets intensifies, this know-how transforms superior alloys like titanium and Inconel into AS9100-compliant marvels—satellite tv for pc thrusters with 0.0005″ tolerances, engine vanes thinner than paper. At XMAKE, we don’t simply meet aerospace requirements; we redefine them, guaranteeing each part soars past expectations.
What’s Aerospace CNC Machining?
Aerospace CNC machining is the artwork and science of crafting flight-critical parts with tolerances measured in microns—the place a human hair’s width is an eternity. This high-stakes course of makes use of computer-controlled mills, lathes, and 5-axis programs to form supplies like titanium, Inconel, and carbon composites into jet engine blades, touchdown gear, and satellite tv for pc frames. In contrast to commonplace CNC, aerospace-grade machining calls for:
- Zero-defect precision: ±0.0002″ tolerances to outlive excessive G-forces and temperature swings (-65°F to three,000°F).
- AS9100 compliance: Rigorous traceability from uncooked materials to closing half, guaranteeing each part is audit-ready.
- Light-weight mastery: Weight reductions that shave kilograms off plane, saving hundreds of thousands in gasoline yearly.
How CNC machining remodeled the aerospace sector?
🛩️ Weight Revolution
CNC machining carves titanium and aluminum into lattice or honeycomb constructions, mimicking bone power at a fraction of the burden. Boeing’s 787 Dreamliner makes use of CNC-milled wing ribs and fuselage panels which might be 30% lighter than conventional builds, slashing annual gasoline prices by $1 million per aircraft. By eradicating extra materials via precision milling, these designs scale back drag and prolong flight vary—key for missions like Airbus’ A350XWB, which flies 8,000 nautical miles nonstop. Lightweighting isn’t simply effectivity; it’s the spine of sustainable aviation.
🚀 Pace to Sky
CNC slashes prototyping instances from months to days. SpaceX’s Raptor engine components, as an illustration, go from CAD fashions to test-ready parts in 72 hours utilizing 5-axis machines. Fast iteration lets engineers take a look at 10x extra designs yearly, accelerating breakthroughs like reusable rocket boosters. Throughout crises—like pandemic ventilator shortages—CNC’s agility converts auto factories into medical gadget hubs in a single day. Pace isn’t a luxurious right here; it’s what retains aerospace forward of worldwide challenges.
🔧 Complexity Unleashed
5-axis CNC machines sculpt “unmachinable” geometries: GE’s LEAP engine nozzles, with 1mm cooling channels woven like spider silk, or blended winglets that minimize vortex drag by 20%. These shapes enhance gasoline effectivity and thrust whereas becoming strict FAA noise guidelines. Hybrid CNC-3D printing programs now construct turbine disks with inner fractal patterns, doubling warmth resistance. Complexity isn’t a hurdle anymore—it’s the blueprint for next-gen flight.
💸 Price Crunch
Automated CNC cells with robotic arms run 24/7, producing F-35 fighter jet components 60% quicker than guide strategies. The 787 Dreamliner’s one-piece composite fuselage sections, CNC-trimmed to perfection, saved Boeing $10 million per aircraft by eliminating 50,000 fasteners. Bulk titanium machining for Airbus A220 frames additionally dropped materials waste from 30% to 7%, proving that precision pays—each in money and carbon.
🛡️ Security First
CNC ensures each aerospace half meets NASA’s 1-in-1,000,000 failure charge rule. Turbine blades bear ultrasonic CNC sprucing to remove microscopic cracks, whereas wing spars are stress-tested through CNC-machined load simulators. Since 1980, engine failures mid-flight dropped 90%—due to CNC’s repeatability. From Mars rovers to helicopter gearboxes, it’s the invisible protect retaining missions (and passengers) secure.
Limitations of CNC machining within the aerospace sector
1. Excessive Prices for Complicated Geometries
Aerospace components like turbine blades with inner cooling channels require 5-axis machines and weeks of machining. Setup, tooling, and materials prices skyrocket, making small batches or prototypes financially daunting. For instance, a single Inconel nozzle can price $10k+ to provide.
2. Materials Machinability Points
Alloys like titanium or Inconel resist warmth however put on down reducing instruments 5x quicker than aluminum. This will increase downtime for device modifications and raises prices. Brittle composites (e.g., CFRP) additionally threat splintering throughout CNC processes.
3. Regulatory and Time Delays
AS9100 compliance calls for rigorous documentation and testing, including weeks to timelines. A single failed stress take a look at means scrapping a $50k titanium wing spar. Pace suffers, even with automation.
Supplies Utilized in Aerospace CNC Machining
Materials | Key Properties | Purposes |
---|---|---|
Robust as metal, half the burden; corrosion-resistant; withstands as much as 600°C | Jet engine parts, spacecraft frames, touchdown gear | |
Light-weight, simple to form; recyclable; cost-effective | Wing panels, satellite tv for pc mounts | |
Withstands excessive warmth (as much as 1,000°C); toughens underneath warmth | Rocket nozzles, turbine blades, hypersonic re-entry shields | |
Stiffer than metal; light-weight; reduces gasoline use by 20% | Airplane wings (Boeing 787), drone our bodies, rotor blades | |
Sturdy; polished end for radar smoothness; magnetic choices out there | Flight controls, engine mounts |
Aerospace CNC machining thrives on supplies engineered to overcome gravity, warmth, and time. Under are the unsung heroes behind flight’s hardest challenges:
Titanium Alloys (Ti-6Al-4V)
Titanium alloys marry the power of metal with half its weight, making them ultimate for jet engine parts and spacecraft frames. Immune to corrosion and temperatures as much as 600°C, they’re the go-to for components like touchdown gear that face salt, stress, and searing warmth each day.
Aluminum Alloys (7075-T6)
Aluminum alloys hold planes mild and agile—suppose wing panels or satellite tv for pc mounts. Straightforward to form and recyclable, they minimize gasoline prices whereas assembly strict eco-standards. Their steadiness of affordability and sturdiness makes them aerospace’s workhorse.
Inconel (718, 625)
Inconel laughs at 1,000°C flames, thriving in rocket nozzles and turbine blades. In contrast to most metals, it toughens underneath warmth, making it good for hypersonic re-entry shields or afterburners that glow white-hot.
Carbon Fiber Strengthened Polymers (CFRP)
CFRP sheets are the key behind Boeing’s 787 Dreamliner wings—stiffer than metal however mild sufficient to slash gasoline use by 20%. Machined into smooth drone our bodies or rotor blades, they redefine what “sturdy and light-weight” means.
Stainless Metal
Chrome steel handles the shakes and rattles of flight controls and engine mounts. Polished to radar-friendly smoothness or magnetic for sensor programs, it’s the quiet spine of dependable aerospace programs.
Aerospace CNC machining transforms these supplies into flight-ready marvels, proving that even the sky isn’t the restrict when science and craftsmanship collide.
Certifications & Requirements for Aerospace Elements
Aerospace components demand certifications that show they’re secure, dependable, and traceable. Right here’s what retains each part airworthy:
AS9100 Rev. D
This international high quality “report card” ensures producers meet NASA and Boeing-level requirements. Consider it as a guidelines for every little thing from titanium bolts to Mars rover components—no defects allowed.
NADCAP (AC7004)
Specialised approval for processes like welding or coatings. If a jet engine blade is heat-treated, NADCAP certifies the oven’s temps have been good—each time.
ITAR Compliance
Required for U.S. protection initiatives. ITAR stops secret tech (like stealth fighter components) from being shared abroad. Even screws want clearance.
ASME BPVC
Guidelines for stress programs like gasoline tanks. Ensures they gained’t burst at 40,000 toes, even when lightning strikes.
ASTM F3122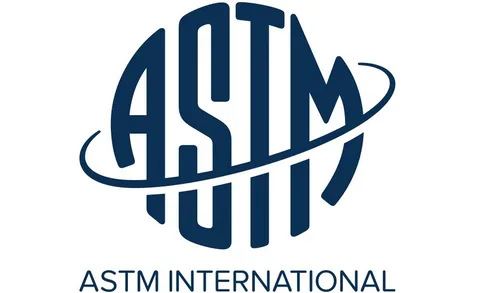
Focuses on titanium components. Assessments their power in icy stratosphere chilly (-65°F) and re-entry-level warmth (1,000°F).
Superior CNC Machining Methods for Aerospace Elements
Aerospace CNC machining leverages cutting-edge strategies to craft parts that defy extremes—from deep-space chilly to hypersonic warmth. Right here’s how innovation meets altitude:
5-Axis CNC Machining
5-axis CNC machines rotate instruments and workpieces alongside 5 instructions concurrently, carving turbine blades with inner cooling channels or satellite tv for pc antenna dishes in a single setup. This eliminates guide repositioning, guaranteeing advanced geometries meet ±0.001″ tolerances. Jet engines and SpaceX’s Starship thrusters depend on this for flawless, light-weight efficiency.
Additive Manufacturing Integration
Combining 3D printing with CNC machining, this hybrid method builds near-net-shape components layer by layer (e.g., titanium gasoline nozzles), then precision-machines vital surfaces. Slashing materials waste by 70%, it’s key for NASA’s Artemis moon rocket parts and drone airframes needing hole, ultra-strong constructions.
Purposes of CNC machining within the aerospace sector
Aerospace CNC machining crafts parts the place failure is just not an choice. Right here’s the place this know-how soars:
1. Jet Engine Parts
CNC machining crafts turbine blades from nickel-based superalloys like Inconel 718, which stand up to temperatures over 1,500°C in jet engines. Utilizing 5-axis CNC programs, producers carve intricate inner cooling channels—some narrower than 0.3mm—to stop melting underneath excessive warmth. These blades spin at 10,000 RPM in engines powering plane just like the Airbus A350 and SpaceX’s Raptor rockets. CNC ensures aerodynamic precision, minimizing gasoline burn whereas maximizing thrust. With out this precision, trendy high-bypass turbofan engines couldn’t obtain their legendary effectivity or reliability.
2. Plane Structural Elements
From titanium wing spars to aluminum fuselage frames, CNC machining balances power and weight in vital airframe parts. The Boeing 787 Dreamliner’s ribbed wings, for instance, are milled from single aluminum blocks, lowering joints and fatigue dangers. CNC’s ±0.001″ tolerances guarantee seamless meeting, whereas light-weight designs minimize gasoline consumption by 15% in comparison with riveted constructions. These components endure many years of pressurization cycles and turbulence, proving that precision isn’t optionally available—it’s the spine of flight security.
3. Touchdown Gear Methods
Touchdown gear parts, like cast metal pistons and titanium trunnions, take up forces equal to 300 tons throughout landing. CNC machines harden these components via processes like shot peening, creating compressive layers that resist cracks. For plane just like the Boeing 777, CNC ensures exacting specs for hydraulic programs and shock absorbers, examined over 50,000 simulated landings. This precision prevents catastrophic failures, even in icy runways or crosswind circumstances, making each touchdown as dependable as the primary.
4. Satellite tv for pc & Spacecraft Methods
CNC machining produces satellite tv for pc thruster housings from titanium and aluminum antenna mounts with sub-0.01mm accuracy—vital for zero-gravity performance. The James Webb House Telescope’s beryllium mirrors, polished to atomic-level smoothness through CNC, detect infrared mild from 13.6 billion light-years away. Photo voltaic panel brackets and sensor mounts are additionally CNC-machined to outlive radiation and temperature swings (-200°C to +150°C), guaranteeing many years of flawless operation in orbit.
5. Cabin Interiors
From carbon-fiber-reinforced seat frames to flame-retardant polyetheretherketone (PEEK) overhead bins, CNC machining blends security and luxury. Enterprise-class lie-flat seats, as an illustration, are CNC-milled from light-weight composites, tailor-made to ergonomic specs. Galley panels and bathroom fixtures are crafted with clean, rounded edges to stop accidents throughout turbulence. Each part meets FAA fireplace security requirements, guaranteeing passenger cabins are as safe as they’re fashionable.
Aerospace CNC machining isn’t nearly constructing components—it’s about engineering belief in each flight, the place millimeters outline margins of security and microns measure the distinction between success and failure.
The way forward for CNC machining within the aerospace sector
CNC machining aerospace components is evolving from a precision device to a visionary power, mixing AI, robotics, and sustainability to redefine flight. Think about self-programming machines that be taught from every minimize, or hybrid programs 3D-printing titanium lattices and CNC-polishing them in a single seamless cycle. Nano-scale machining might craft sensors thinner than spider silk, embedded in wings to foretell put on mid-flight. In the meantime, inexperienced machining will slash carbon footprints by recycling 95% of metallic waste.
Able to pioneer this new period? Associate with XMAKE—the place digital manufacturing meets aerospace ambition. Let’s code the way forward for flight, one precision-cut innovation at a time. Your blueprint? Our experience. The sky’s not the restrict; it’s the beginning line. 🛠️✨
Take into account Partnering with XMAKE
- Finish-to-Finish Help: From design optimization to closing manufacturing.
- State-of-the-Artwork Machines: Newest 5-axis programs for advanced geometries.
- Trade-Confirmed Outcomes: Trusted by leaders in aerospace, power, and past.
Able to pioneer this new period? Associate with XMAKE—the place digital manufacturing meets aerospace ambition. Let’s code the way forward for flight, one precision-cut innovation at a time. The sky’s not the restrict; it’s the beginning line. 🛠️✨
Associated submit it’s possible you’ll curiosity
1.All the pieces You Ought to Learn about Swiss CNC Machining in 2025|XMAKE
2. 9 Purposes of Plastic Injection Molding for Medical Gadgets in 2024
3. 10 Purposes of Metallic Injection Molding in Medical Gadgets in 2024
4.9 Newest Purposes of 3D Printing in Aerospace in 2024
FAQ
1. Is precision vital when CNC machining aerospace components?
Completely. Aerospace parts face excessive stress, warmth, and vibration—suppose turbine blades spinning at 10,000 RPM or rocket nozzles enduring 3,000°C. A single micron-level error can unbalance an engine or crack a gasoline line. CNC machining delivers tolerances as tight as ±0.001mm, guaranteeing components meet NASA/AS9100 security requirements. With out this precision, trendy jets couldn’t obtain their 99.9% reliability charge.
2. What Abilities Are Important for Mastering CNC Machining?
- CAD/CAM fluency: Turning 3D fashions into error-free toolpaths.
- Materials know-how: Understanding how alloys like titanium behave underneath reducing forces.
- Precision measurement: Utilizing micrometers and CMMs to confirm sub-0.01mm accuracy.
- Downside-solving: Tweaking feeds/speeds to stop device chatter on thin-walled components.
- Adaptability: Studying hybrid tech like CNC-3D printing combos.
3. Why is complexity an asset within the aerospace sector?
Complicated designs unlock breakthroughs. For instance, GE’s LEAP engine nozzles have 3D-printed lattice constructions inside, CNC-finished to deal with 1,500°C flames whereas utilizing 15% much less gasoline. Equally, Airbus’ curved winglets scale back drag by 20%. Superior 5-axis CNC machining makes these once-“not possible” shapes routine, proving that in aerospace, complexity isn’t a hurdle—it’s the trail to smarter, greener flight.
Reference
1. Altintas, Y. (2012). Manufacturing Automation: Metallic Chopping Mechanics, Machine Device Vibrations, and CNC Design (2nd ed.). Cambridge College Press.
Foundational textual content on 5-axis machining dynamics and aerospace-grade precision.
2. AS9100D:2016. High quality Administration Methods – Necessities for Aviation, House, and Protection Organizations.
World commonplace for aerospace CNC half traceability and defect prevention.
3. Budinski, Okay.G., & Budinski, M.Okay. (2010). Engineering Supplies: Properties and Choice (ninth ed.). Prentice Corridor.
Covers titanium, Inconel, and CFRP machining challenges in aerospace.
4. Nationwide Aeronautics and House Administration (NASA). (2021). Structural Design and Take a look at Standards for Spaceflight {Hardware}. NASA-STD-5001B.
Mandates CNC tolerances for crewed mission parts.