Most manufacturing corporations, nonetheless small, have objectives to increase their market share and enhance their income. Whereas there are a number of methods to try this, scaling up manufacturing could also be the very best plan of action. The article explains how scaling up works, what to anticipate, and the right way to plan for profitable progress.
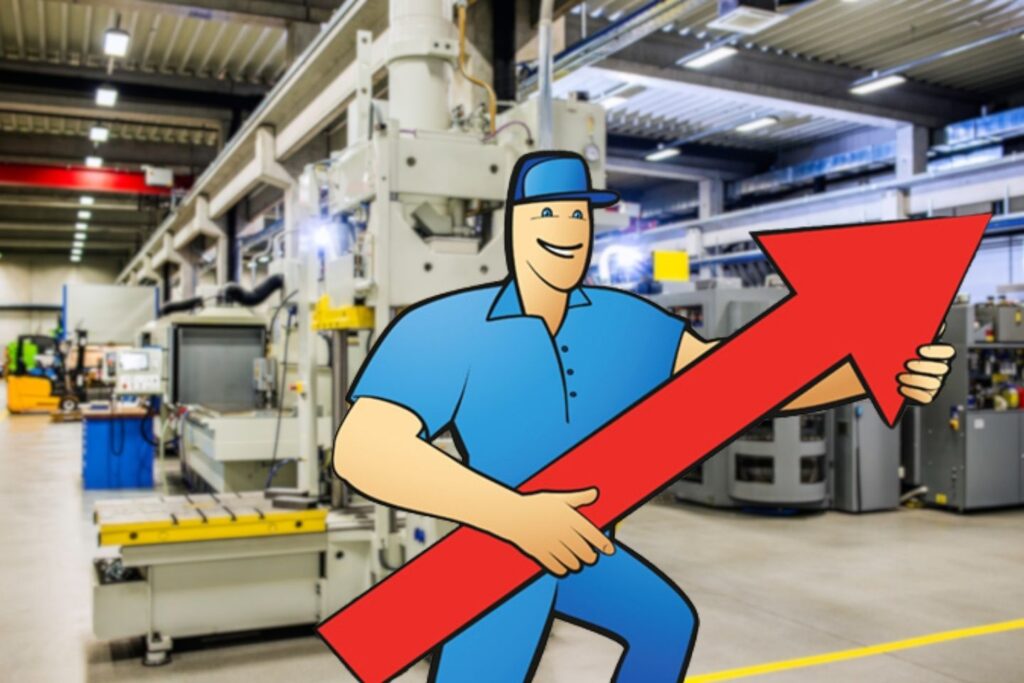
What’s scaling up in manufacturing?
Progress and scaling are sometimes used interchangeably. In actuality, they’re two totally different strategies of rising income and market presence. It’s good for SMEs, particularly producers, to grasp the distinction.
Progress is a course of the place each income and prices enhance proportionally. That implies that whereas income will increase, the revenue margin stays pretty constant. That is regular, however may trigger eventual monetary pressure if prices outpace income.
When an organization is scaling up, nonetheless, it’s potential to extend income with no important corresponding rise in prices and useful resource use. Scaling up is the best choice for strategic long-term enterprise sustainability and profitability. As an alternative of remaining stagnant, revenue margins may really enhance shortly.
Key traits of scalable manufacturing
The watchword for scaling up a producing enterprise is manufacturing effectivity. A scalable manufacturing operation could have manufacturing processes in place that may simply adapt to larger demand. This not solely pertains to the store ground, however to labor, administration, and financials as properly.
Strategies of retaining prices beneath management are set in place, and the corporate can reap the benefits of what is named the economies of scale. Because of this the fee per unit decreases the extra the corporate manufactures. This may be tracked and quantified, notably if the corporate is utilizing a course of costing technique for its manufacturing course of. Whereas the cost-per-unit decreases, a high-quality product remains to be produced.
Moreover, most producers scaling up will strategically use course of automation and varied applied sciences to optimize processes and scale back labor prices.
Indicators {that a} enterprise is able to scale
If an organization fastidiously tracks its effectivity, output, gross sales, and manufacturing orders, there will likely be robust indicators that it’s able to enter scaling mode. Two of them are:
- Constant market demand exceeding present manufacturing capability.
- Confirmed market alignment with a steady buyer demand for the product.
When product demand begins to outpace product provide, the corporate wants to start earnest planning for strategically scaling up their complete operation. They need to start by growing manufacturing processes and methods that can enhance workflow effectivity. They need to take into account these applied sciences and automation that may enhance manufacturing capability whereas nonetheless sustaining product high quality.
The corporate must also create and implement operational platforms that can accommodate progress with no proportional enhance in course of prices.
Frequent challenges in scaling manufacturing processes
Sadly, there’s no change to flip or a straightforward button to push to place a producing enterprise in scaling mode. As with all progress, there are some challenges to beat.
Operational challenges
Capability constraints aren’t restricted to the manufacturing line. Whereas there could also be a necessity for brand spanking new manufacturing line gear to deal with the rising demand for a product, warehousing might also want consideration. Merchandise could depart the warehouse shortly however an elevated manufacturing quantity additionally requires more room for uncooked materials stock. This might be solved by including extra area, or by enhancing the prevailing areas, i.e. via vertical storage choices.
It’s additionally necessary to keep up product high quality, even beneath elevated output. Whereas human inspectors are all the time crucial, inspection automation can streamline the high quality management course of.
A rise in manufacturing additionally leaves an organization susceptible to produce chain issues. Cautious planning and provide chain administration are crucial to keep up a fluid provide of uncooked supplies. When partnerships are cast with suppliers and logistics corporations, these accountable for the stock and manufacturing course of should be sure that the availability chain companions can scale up as properly.
Monetary hurdles
When scaling up, managing money move for enlargement investments is essential. The choice-making course of consists of balancing operational prices with income progress. It’s additionally potential that the producer should safe extra funding for brand spanking new gear and expertise to scale manufacturing. A wholesome monetary image is important to point out legitimacy for those who want extra funding.
Workforce administration points
Scaling as much as meet elevated market demand could require hiring and coaching a bigger workforce, however this isn’t all the time the case. Cross-training for various manufacturing processes can allow staff to deal with a number of duties as wanted, permitting a extra fluid workforce.
Expertise and infrastructure limitations
For services nonetheless utilizing legacy manufacturing methods, integrating new automation and digital instruments could be difficult.
Older producers could discover their bodily services, expertise infrastructure, and manufacturing strains aren’t conducive to scaling up. Plans to work round these obstacles should be fastidiously studied for feasibility, with varied choices researched.
As manufacturing corporations implement a extra digitally-driven system or methods, they’ll have to take steps to make sure IT and cybersecurity readiness. A cloud-based system may help guarantee this, whereas additionally permitting necessary knowledge to be shared with those that want entry.
Greatest practices for scaling manufacturing processes
Listed below are some greatest practices for implementing manufacturing operations to scale up and meet elevated market demand.
Strategic planning and objective setting means defining clear, measurable targets for scaling up. The corporate will need to have an actionable roadmap for enlargement, in addition to a transparent evaluation of market situations and aggressive positioning.
Course of optimization and standardization embrace figuring out and eliminating inefficiencies and bottlenecks in manufacturing workflows. Lean manufacturing methods enhance effectivity and scale back waste within the manufacturing course of. Standardized high quality management processes preserve the consistency very important for safeguarding product high quality, particularly as product volumes enhance.
Expertise and automation funding would possibly embrace leveraging robotics and AI to enhance effectivity. Sensible manufacturing methods and using IoT (Web of Issues) present a related surroundings. This real-time knowledge assortment and evaluation assists in efficient decision-making.
As well as, think about using preventive upkeep to reduce or keep away from disruptions to your workflow.
Provide chain and stock administration embrace strengthening present provider relations and diversifying your sourcing choices. These present workarounds throughout provide chain disruptions. Discover suppliers that may ramp up as you scale up. Together with uncooked materials provider administration, correct stock management is important.
Actual-time stock monitoring and correct forecasting of future market calls for can allow a producing firm to make use of just-in-time stock methods to maintain from overstocking supplies. Exact stock management can even forestall stockouts.
How manufacturing ERP helps you scale up
The times of computer-based spreadsheets are just about gone. Whereas they served an awesome function, most manufacturing processes shortly outgrow their capabilities. As most spreadsheets are up to date manually and shared with different departments, that inefficiency alone generally is a stumbling block to scaling up.
Customers usually report that implementing manufacturing software program has enabled them to supply bigger volumes and fill extra orders with no corresponding enhance in labor hours.
For one, manufacturing ERP software program drastically reduces the time spent on workplace duties equivalent to manufacturing planning and scheduling, workforce administration, and buying. With stock management, calendar scheduling, and manufacturing planning baked into the system, managers are capable of shortly decide materials and labor necessities and lead occasions for manufacturing orders, making certain correct deliveries and buyer satisfaction.
Optimizing stock and provide chain administration is a serious part of producing ERP options, serving to scale back waste by enhancing inventory management. These software program methods make sure the real-time monitoring of uncooked supplies and completed items, enabling you to know precisely what you have got in inventory and the place. This can be a large step ahead towards eliminating stockout and overstocking challenges.
Facilitating data-driven decision-making is a key profit of producing ERP software program options. By utilizing real-time analytics and efficiency insights offered by the system, managers can predict demand traits, establish manufacturing bottlenecks, and optimize useful resource allocation. Together with course of and manufacturing management, in addition they enhance monetary planning and budgeting by exactly monitoring manufacturing prices.
Guaranteeing scalability and future progress is a key profit of those software program workhorses. They simply adapt to elevated manufacturing volumes, retaining the workflow easy and heading in the right direction. Ought to new processes be added for speedy prototyping of proposed new product strains, manufacturing ERP software program can simply alter for seamless integration.
Lastly, they supply long-term visibility into your processes, adapting because the producer begins and continues to scale up. This may future-proof what you are promoting progress.
Key takeaways
- Scaling is distinct from progress – It focuses on rising income whereas minimizing value enlargement. Progress often entails proportional will increase in value and income.
- Manufacturing scalability requires operational effectivity – Streamlining processes, automating manufacturing, and optimizing useful resource utilization are important when scaling up manufacturing processes and output.
- Frequent challenges embrace operational bottlenecks, monetary constraints, and workforce adaptation – Companies should strategically plan for enlargement, working to eradicate these roadblocks.
- Expertise and automation play a vital function in scaling success – Sensible manufacturing, ERP methods, and data-driven decision-making complement scalability by monitoring the manufacturing course of in actual time.
- Provide chain administration is significant – Strengthening provider relationships and optimizing stock assist preserve seamless manufacturing throughout scaling. Suppliers should be capable to accommodate your enhance uncooked materials calls for.
- ERP options allow scaling – They combine operations, enhance effectivity, and supply knowledge visibility company-wide.
By specializing in strategic scaling fairly than simply progress, producers guarantee long-term success. Implementing greatest practices and leveraging ERP expertise, manufacturing corporations scale sustainably into the long run. Growing their profitability with out sacrificing revenue margins solidifies their increasing place within the manufacturing trade.
Incessantly requested questions (FAQ)
The timeline for scaling up depends upon a number of elements, together with the complexity of manufacturing, the extent of funding wanted, and the corporate’s readiness by way of methods and workforce. For some corporations, it might take a number of months to some years to completely scale operations whereas making certain high quality and effectivity.
Producers ought to prioritize ERP methods with strong manufacturing planning, real-time stock monitoring, provide chain administration, and customizable reporting options. Integration capabilities, scalability, and user-friendliness are additionally vital to make sure the system grows with the enterprise.
Sustaining strict high quality management processes, investing in automated inspection methods, and standardizing manufacturing procedures assist reduce high quality dangers. Common audits and steady worker coaching additionally guarantee product requirements stay constant as manufacturing volumes enhance.
You might also like: What Is Value per Unit and Scale back It?