US producers could must rethink their method to developing new manufacturing facility websites to fulfill rising demand effectively.
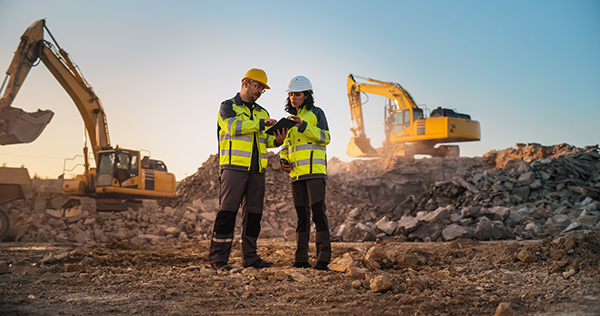
By Erikhans Kok, McKinsey & Firm
As international commerce dynamics shift, the case for localizing manufacturing is getting stronger. Rising volatility in tariffs and commerce insurance policies, evolving incentives for home manufacturing, and the realignment of worldwide commerce corridors are pushing firms—notably in the USA—to carry manufacturing nearer to dwelling. But, whereas nearshoring guarantees larger provide chain resilience and strategic benefit, the fact of constructing new factories is much tougher.
Firms throughout sectors—from semiconductors and electronics to aerospace—are beneath stress to ramp up manufacturing and reorganize their footprint, but many wrestle to scale their infrastructure on the required tempo. Lower than half of all main capital initiatives are delivered on time and on finances. Years of deal with progress via acquisitions and community consolidation over in-house enlargement, have left even chief manufacturing officers with little to no expertise in growing new websites.
To bridge this capability hole, producers could must shift their mindset from typical, sequential development processes to an built-in, modular, and tech-driven method. By rethinking how factories are constructed, firms might obtain vital enhancements.
The capability hole: A structural bottleneck
In recent times, industrial enlargement within the US has been marked by guarantees of high-ambition funding. One North American semiconductor producer, as an example, pledged billions towards a brand new fabrication plant, whereas a shopper electronics producer sought to increase capability to a website that was greater price than its conventional low-cost-country base.
But, regardless of the injection of capital, the event of recent factories is transferring extra slowly than they may, with the common capital mission working roughly 60 p.c over schedule and greater than 70 p.c over finances (Exhibit 1).
Among the primary causes for gradual tempo of supply embody:
- Labor shortages: The restricted availability of extremely expert development and engineering employees makes it troublesome to employees massive initiatives.
- Provide chain limits: Delays in scheduling the supply of key supplies, together with logistical bottlenecks, are slowing down development timetables.
- Regulatory impediments: More and more advanced environmental, zoning, and security laws have lengthened approval timelines, delaying mission begin dates.
- Inefficient mission administration and design processes: Conventional mission execution strategies, reliance on bespoke designs, and poor coordination amongst stakeholders result in delays and finances overruns.
The outcome? The vast majority of manufacturing facility initiatives grow to be longer and much costlier than initially deliberate. As well as, the manufacturing facility development delay equates to manufacturing delay—which interprets to misplaced revenues and subjecting firms to potential lack of market alternatives.
Exhibit 1
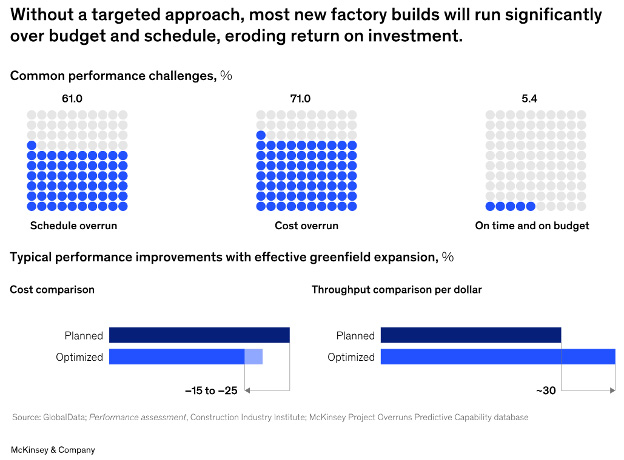
Redesigning manufacturing facility development
Closing the capability hole requires a considerable change in manufacturing facility development and constructing design. Prime producers are discovering revolutionary methods to speed up timelines and scale back dangers, with 4 approaches standing out.
Transferring to prefabricated and modular development
As an alternative of constructing every part on the job website, firms can velocity up development by using modular and prefabricated constructing items. This method entails constructing key sections of a manufacturing facility in off-site vegetation after which assembling them on the vacation spot website. It helps decrease peak manpower calls for on website.
The semiconductor producer talked about above used superior development applied sciences, together with the newest modular-building methods, to mitigate dangers, shortening development intervals by months and decreasing inefficiencies on website. The corporate additionally employed generative scheduling and efficiency transparency instruments to optimize the development timeline and scale back prices.
Making use of digital twins, AI planning, and Business 4.0
One of many primary causes for price overruns and delays in manufacturing facility development is n of the development schedule throughout the mission. altering scope late within the mission, particularly to accommodate adjustments to the structure or add new flexibility. Firms can remove such dangers by leveraging Business 4.0 applied sciences, corresponding to digital twin expertise—digital replicas that replicate each element of the constructing course of in actual time (Exhibit 2).
A medical-products firm used a digital twin to optimize the structure of a brand new plant for its high-mix, high-volume product portfolio. It simulated future manufacturing, enabling engineers to construct in extra flexibility and decrease the impression of frequent changeovers—resulting in a 20 p.c enhance in general tools effectiveness and gross margin will increase of practically 50 p.c. A multinational shopper electronics producer doubled throughput and diminished price per unit by 30 to 40 p.c by implementing Business 4.0 applied sciences throughout manufacturing facility design.
Moreover, some producers are implementing related manufacturing strains with sensors and digital work directions to enhance provide chain coordination, guaranteeing smoother ramp-up instances and higher effectivity.
Exhibit 2

Parallelizing workstreams to compress timelines
One of many largest inefficiencies in manufacturing facility development is the standard sequential method—the place every section of constructing occurs one after the opposite. As an alternative, firms might have to think about using parallelized work streams, the place a number of phases advance concurrently.
The aforementioned semiconductor producer did this very successfully. It optimized its manufacturing facility construct by splitting up massive work packages in order that a number of contractors might work in parallel on-site. Utilizing generative scheduling fashions, it examined various development sequences and labor reallocations, figuring out over 90 optimization alternatives that helped scale back timelines and prices.
Bettering provide chain coordination and administration
Even when manufacturing facility development in full, poor provide chain coordination can result in delays within the manufacturing output from new manufacturing facility initiatives. Bettering and strengthening the provision chain earlier than development is accomplished can forestall disruptions and preserve manufacturing on schedule.
One aerospace and protection producer performed an in-depth evaluation of provider capability, geographic footprint, and logistics to make sure that its suppliers might meet projected demand. The semiconductor fab’s improved procurement coordination managed to triple the variety of accomplished RFPs and align procurement with the development schedule. Moreover, it saved greater than $50 million by optimizing workforce allocation via its labor technique.
A blueprint for developing factories sooner or later
Closing the manufacturing capability hole requires reimagining conventional development strategies and embracing a extra adaptable, technology-driven method. With modular development, digital twins, parallelized workstreams, and provide chain optimization, producers can dramatically scale back prices, speed up timelines, and scale back execution threat.
This shift is about making companies able to scaling manufacturing capability in time to fulfill surging market demand. The factories that may replace their manufacturing facility development fashions will likely be forward of the sport, whereas those caught in outdated fashions of development threat falling behind.
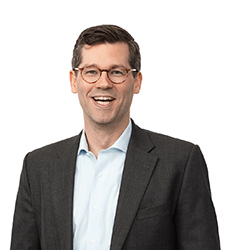
In regards to the Writer:
Erikhans Kok is a senior companion in McKinsey’s Houston workplace and the worldwide co-leader of McKinsey’s Capital Excellence follow.
He gives deep experience in optimizing capital mission portfolios in addition to growing and delivering mega capital initiatives, together with stress testing enterprise instances, validating price and schedule estimates, contracting technique, design optimization, all the best way into mission discipline execution.
Learn extra from the writer:
Smarter progress, decrease threat: Rethinking how new factories are constructed | McKinsey & Firm, February 2025
How capital expenditure administration can drive efficiency | McKinsey & Firm, June 2022
Capturing the net-zero alternative with portfolio synergies | McKinsey & Firm, April 2022
The put up The Future Of Manufacturing facility Development: Rebuilding At House appeared first on Business At this time – Chief in Manufacturing & Business Information.